45+ Inventory Management KPI Examples
Inventory management isn't just about counting items on shelves. In our modern, dynamic marketplace, it's a strategic ballet – a balance between supply and demand, ensuring that products are available when and where customers want them, without tying up excess capital in stock. When executed effectively, inventory management becomes the silent maestro of a harmonious supply chain, driving profitability, sustainability, and customer satisfaction.
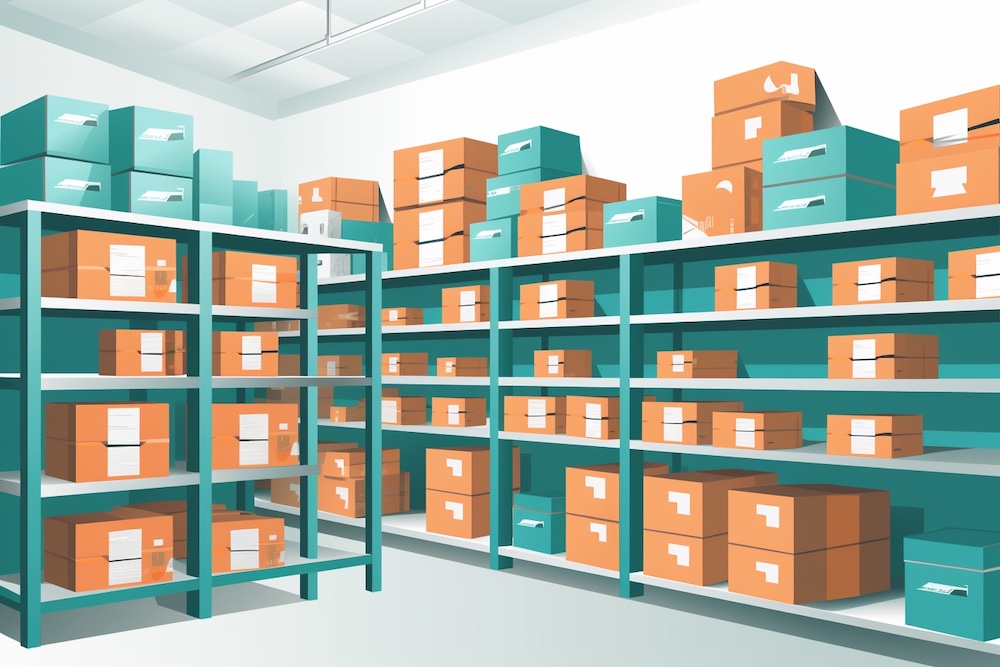
Deciphering Inventory KPIs
At its core, inventory is a narrative, telling the tale of a product's journey from supplier to consumer. Key Performance Indicators (KPIs) translate this narrative into a language businesses can understand and act upon. For someone not deeply entrenched in numbers, it might seem overwhelming, but when deciphered, these metrics are simply the pulse points of a company's inventory health. They can illuminate the nuances of turnover rates, shed light on stockout risks, and highlight opportunities to optimize warehousing costs.
The Strategic Dimension of Inventory KPIs
Inventory isn't static; it's a flowing, dynamic entity that requires agile management. Strategic inventory KPIs help businesses anticipate market shifts, making them proactive rather than reactive. This is about not just minimizing holding costs but maximizing service levels and ensuring that the voice of the customer echoes through the supply chain. It's a delicate equilibrium between having enough and having too much, and the right KPIs act as the fulcrum.
In today's complex supply chain landscape, every department from purchasing to sales should understand inventory metrics. This cross-functional synergy ensures alignment, facilitates swift decision-making, and nurtures a culture of continuous improvement.
Tailoring the Right KPIs for Your Inventory Objectives
The uniqueness of each business, influenced by its goals, supply chain intricacies, and market landscape, means there's no universal set of inventory KPIs. But certain tenets can guide your selection:
- Customer-Centricity: The best inventory KPIs resonate with customer needs, ensuring products are available without delays or stockouts.
- Actionability: A metric without actionable insights is a number without meaning. KPIs should directly influence strategy and operations.
- Relevance in Real-Time: The rapidity of today's market means yesterday's KPIs might be obsolete today. Refresh, revisit, and recalibrate regularly.
On KPI Examples, the community offers a beacon, marking out the most pertinent KPIs for inventory management. It's a space where professionals from across the globe converge, sharing insights and upvoting the KPIs resonating most with the challenges and opportunities they face.
Most Popular Inventory Management KPIs for 2025
Delve into the inventory KPIs that industry professionals have flagged as indispensable. Understand their nuances, calculations, and applications in depth.
Stockouts in Period #
The number of times stock was unavailable when requested in a specific period. Frequent stockouts can lead to lost sales and decreased customer satisfaction.
Formula
Total Stockouts in Period
Example
If stock was unavailable 10 times in a month, there were 10 stockouts.
Rate of Correctly Picked Line Items %
The percentage of items correctly picked from inventory for order fulfillment. Higher percentages indicate effective picking processes and reduced errors.
Formula
(Number of Correctly Picked Items / Total Items Picked) x 100
Example
If 980 out of 1000 items are picked correctly, the rate is 98%.
Inventory Shrinkage as Percentage of Inventory Value %
Represents the reduction in the recorded inventory value that is not accounted for by sales. This includes theft, damage, miscounts, and other losses. Understanding shrinkage helps businesses adjust security measures, refine inventory processes, and improve profitability.
Formula
(Value of Lost Inventory / Initial Inventory Value) x 100
Example
If the initial inventory value was $50,000 and the value of lost inventory is $1,000, the shrinkage rate is 2%.
Inventory Turnover #
This KPI measures how often an organization's inventory is sold and replaced over a given period. A high turnover indicates efficient inventory management and sales processes, while a low turnover might mean poor sales or excessive inventory.
Formula
Cost of Goods Sold / Average Inventory
Example
If the cost of goods sold is $1,000,000 and average inventory is $200,000, the inventory turnover is 5 times.
Economic Order Quantity #
EOQ provides the ideal order quantity to minimize costs related to order, holding, and shortage costs. It's foundational for efficient inventory management.
Formula
Square Root of [(2 x Demand x Order Cost) / Holding Cost]
Example
For an annual demand of 1200 units, order cost of $5, and holding cost of $2 per unit, the EOQ is about 49 units.
A Comprehensive Dive into Inventory KPIs
Explore an exhaustive list of inventory management KPIs. Each metric is paired with a succinct summary, but don't stop there – click on any KPI to unlock its complete story, formula, and real-world application.
Costs & Value
- Average Inventory Value: This indicates the average monetary value of inventory held over a period.
- Carrying Costs, Finished Goods: These are the costs associated with holding inventory that's ready for sale.
- Gross Margin Return on Inventory Investment: This metric evaluates the return on every dollar invested in inventory.
- Holding Cost per Unit: Represents the average cost to hold each unit of inventory.
- Insurance Costs as Percentage of Inventory Costs: Indicates the portion of inventory costs represented by insurance.
- Inventory Holding Costs as Percentage of Gross Sales: This KPI measures the proportion of gross sales that's consumed by the costs of holding inventory.
- Inventory Holding Costs as Percentage of Inventory Value: Represents the proportion of inventory value consumed by holding costs.
- Value of Obsolete Stock: This KPI measures the monetary value of stock that's no longer relevant or sellable.
Demand Forecasting
- Forecast Accuracy: Indicates how close the forecasted demand was to the actual demand.
- Forecast Bias: Represents the tendency of the forecasts to consistently be higher or lower than the actual demand.
- Mean Absolute Percentage Error: Mean Absolute Percentage Error (MAPE) provides an average of the absolute percentage errors in the forecast.
- Rate of Stockouts Due to Forecast Inaccuracy: Measures the number of times stockouts occurred due to errors in demand forecasting.
Efficiency & Performance
- Average Dock-to-Stock Time: This metric indicates the average time it takes for goods to move from the receiving dock to available inventory.
- Economic Order Quantity: EOQ provides the ideal order quantity to minimize costs related to order, holding, and shortage costs.
- Fill Rate: Represents the percentage of customer orders that are fulfilled from stock on hand.
- Frequency of Canceled Orders: Highlights the number of orders canceled, either due to stockouts or other operational inefficiencies.
- Frequency of Emergency Orders: This KPI measures how often emergency orders are placed, indicating potential inefficiencies in order prediction or supplier reliability.
- Order Lead Time: The time it takes from placing an order to its receipt.
- Rate of Correctly Picked Line Items: The percentage of items correctly picked from inventory for order fulfillment.
Inventory Accuracy & Integrity
- Cycle Count Accuracy: Assesses the accuracy of inventory counts done periodically (daily, weekly, monthly) compared to the inventory management system records.
- Inventory Accuracy: Measures the percentage comparison of the physical count of inventory items to the recorded amount in the inventory management system.
- Inventory Location Accuracy: Determines how often inventory items are found in their designated locations within a warehouse or storage facility.
- Inventory Shrinkage as Percentage of Inventory Value: Represents the reduction in the recorded inventory value that is not accounted for by sales.
- Rate of Inventory Items Incorrectly Located: Assesses the rate at which items are not found in their designated or recorded locations.
- Rate of Inventory Items with Incorrect Stock Balances: Calculates the rate at which the recorded stock balance does not match the actual physical count.
Safety, Risk & Waste Management
- Damaged Stock Rate: Represents the percentage of stock that gets damaged.
- Inventory to Obsolete Goods Ratio: Indicates the relation between the total inventory and obsolete items.
- Rate of Expired Items to Inventory Value: This KPI measures the percentage of the inventory's value that consists of expired items.
- Rate of Safety Stock Used: Indicates the portion of safety stock that's utilized, offering insights into whether the safety stock levels are appropriate.
- Size of Safety Stock: Safety stock is the quantity of stock held to guard against stockouts.
- Stock Obsolescence Rate: Shows the rate at which inventory becomes obsolete.
- Value of Items Stolen from Inventory: The total value of inventory items stolen.
Stock Levels & Turnover
- Average Age of Inventory: Represents the average number of days items stay in inventory before being sold.
- Backorder Rate: The ratio of items that are ordered but currently out of stock to total sales, indicating how often sales cannot be immediately fulfilled.
- Inactive Inventory as Percentage of Inventory Value: Measures the value of items that have not been sold or used for a long period, indicating potential dead stock that ties up capital.
- Inventory Days of Supply: Indicates how many days the current inventory will last at the current sales rate without new stock.
- Inventory Turnover: This KPI measures how often an organization's inventory is sold and replaced over a given period.
- Sell-through Rate: Measures the amount of inventory sold in relation to the amount received.
- Stock Availability Rate: Indicates the percentage of time items are available in stock when requested, pointing to the effectiveness of inventory management.
- Stock Cover: The duration of time the current inventory will last given the sales rate.
- Stockouts in Period: The number of times stock was unavailable when requested in a specific period.
Supplier Performance
- Supplier Compliance Rate: Measures how frequently a supplier adheres to contractual terms, industry standards, and regulatory guidelines.
- Supplier Defect Rate: Represents the percentage of received goods from a supplier that are defective.
- Supplier Lead Time Variability: Indicates the variation in lead time for orders from a particular supplier.
- Supplier On-time Delivery Rate: Measures the frequency at which suppliers deliver orders within the stipulated timeframe.
Technology & Modern Methods
- Automated Inventory Ratio: The percentage of inventory management tasks that are automated, enhancing efficiency and reducing manual errors.
- Inventory System Downtime: The amount of time the inventory management system is unavailable due to technical issues.
- Percentage of Duplicate Stock Numbers: Represents the percentage of inventory items with duplicate stock numbers.
- Rate of Items Tracked with RFID: Indicates the proportion of inventory items tracked using Radio Frequency Identification (RFID).
Final Thoughts
In an era where the supply chain is both a challenge and a competitive differentiator, inventory management stands at its heart. Harnessing the right KPIs offers not just visibility but foresight, allowing businesses to maneuver with agility and precision. As we navigate the intricacies of 2025, let these metrics be your compass, guiding you towards supply chain excellence and stellar customer satisfaction.
Keen on exploring KPIs across other domains? Dive into our expansive category list and let data sculpt your success narrative.